İşletmelerde Görülen 7 Büyük Kayıp
Bir önceki yazımızda Toyota Üretim Sistemi (TPS) nde ifade edilen en temel 7 kayıp (MUDA) tan bahsetmiş ve bu yazımızda da bu kayıpların nasıl oluştuğunu anlatacağımızı söylemiştik. Kayıplarımızı analiz etmeye “Fazla Üretim”den başlıyoruz:
KAYIPLAR HERYERDE AMA GÖREBİLİYOR MUYUZ? |
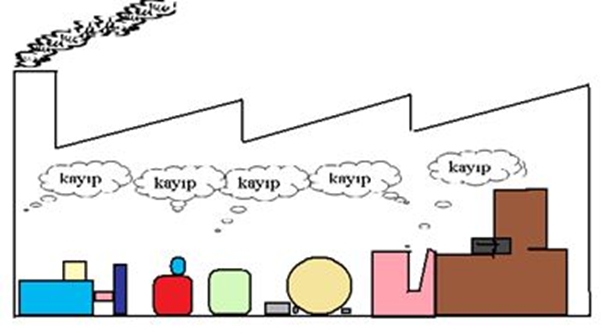
1.Fazla Üretimden Kaynaklanan KAYIP
Fazla Üretim; Pazarın, müşterinin istediğinden fazla üretmek anlamına gelir.
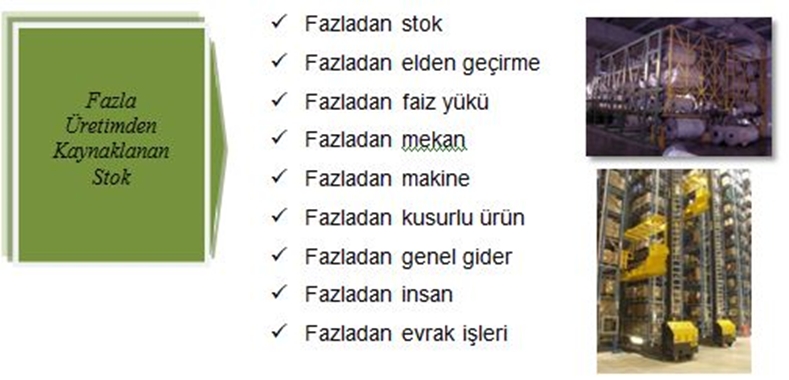
Fazla üretim birçok problem yaratır ve problemlerin gerçek nedenlerini gözlerden saklar.
İşletmelerde tedarikçi-müşteri ilişkisi olmalı, müşteri tarafından talep edilen miktarda, yüksek kalitede, düşük maliyette ve gereken zamanda ürettiğimizden emin olmalıyız.
Fazla stoğun diğer zararları
- Herkes (operatörler, bakımcılar, makineler) çalışır gözükür.
- Zihinler dağılır. İşletmede her şeyi net göremezsiniz. İyi- kusurlu ürün; mamul stok-yarı mamul stok; İşlem görecek malzeme- müşteri bekleyen malzeme…
- Raporlar aldatıcı olur.
- Fazla ekipmana ihtiyaç duyulur. Sehpalar, taşıma araçları vs.
İspanya’da gezdiğim alüminyumda dünya devi olan bir firmada yarı mamul alüminyum bobinleri stokladıkları bir alanı gördüm. Nerdeyse hiç stok yoktu. Bizi gezdiren yöneticiye “ne güzel stok alanınız var” dedim. Adına “high bay storage “dediğimiz çok katlı, otomatik yükleme sistemi olan çok büyük bir stok alanı idi. Adam acı acı gülümsedi. “Boşuna yaptık bunu” dedi. “Niçin” ? dedim. “Bizim o kadar stoka, dolayısı ile bu kadar da büyük bir stok alanına ihtiyacımız olmamalı idi, gördüğünüz gibi artık fazla stok tutmuyoruz” diye cevap verdi.
2.Bekleme Zamanından Kaynaklanan KAYIP
Bekleme zamanı kaybı kolay fark edilir. Çünkü makinenin durduğunu herkes görür.
“Fazla üretim yapmak yerine makine durmalıdır”
Böyle olunca kapasite daha iyi değerlendirilir ve durum daha kolay kontrol altına alınır. Özellikle patron işletmelerinde bu durumu patrona anlatmak çok zordur. Tecrübe ile görülmüştür ki makinelerin gerekirse durdurulması ve böylece sipariş miktarı, sipariş miksi ya da kötü planlama benzeri problemlerin açıkça görülmesinin sağlanması kolay bir karar değildir. Çünkü bunu patrona anlatamazsınız, ya da anlatmak istemezsiniz. Çünkü makinenin durmasında organizasyonun birçok biriminin şöyle ya da böyle bir kusuru olacaktır. Bunun da üst yönetimlerce bilinmesi pek hoş olmaz.
Çalışan makineyi gözlemleyen operatörlerin bu işi geçmişte genelde kayıp sayılmazdı. Ancak bu pasif faaliyeti de KAYIP (gizli kayıp) saymak durumundayız.
Bir hata olduğunda makineyi durduran ya da ikaz eden sistemler son derece geliştiğinden bunlar kullanılarak operatör ve yardımcılara başka işler yaptırılabilir.
Böyle bir sistem yoksa operatörler küçük sorunları hallederler (sensörleri aldatmak, iptal etmek gibi) ve amirlerin bulardan haberi bile olmaz. Böylece zaman içinde kişiye bağlı prosesler ortaya çıkar. Amirler bazı hata ve işlemlerin farkına vardığında çoğu zaman iş işten geçmiş, ya malzeme hatalı olmuştur ya da makine arıza yapmıştır.
3.Taşıma KAYBI
- İşletmeler dikkatli bir bakış açısı ile incelendiğinde üretim ya da hizmette kullanılan malzemelerin ne kadar da gereksiz yere bir yerden bir yere hareket ettirildiği görülür.
- Kötü planlanmış yerleşimlerde malzeme taşınması uzun mesafeler olabilir. Malzemenin işletmedeki kat ettiği yolun öğrenilmesi çoğu kez insanları şaşırtır.
- Yeni gelen malzemenin hangi ambarda nerede depolanacağı, hangi üretim hattına verileceği, ne zaman verilmesi gerektiği belli olmalıdır.
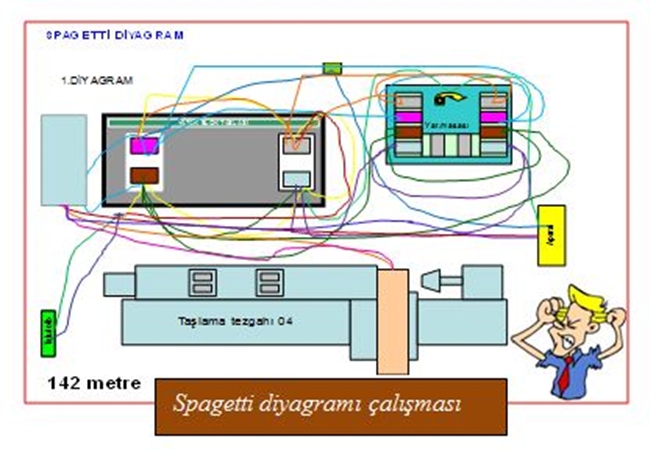
Taşıma Kaybını ortadan kaldırmak için;
- Yerleşimde
- Süreçlerin koordinatlarında
- Taşıma yöntemlerinde
- Bina bakımında ve
- İşyeri organizasyonunda …
iyileştirme gerekir.
Operatörlerin gün boyunca yaptığı işler takip edilerek bir spagetti diyagramı çıkarılırsa kalıp, anahtar, vinç kumandası vb. malzemeleri almak ya da çalışacağı yarı mamul malzemeleri almak, getirmek için ne kadar taşıma kaybı olduğu net olarak görülebilecektir.
4.İşleme Kaybı
- Malzeme işlenirken makine parametrelerinin yetersiz olması nedeni ile yavaş çalışma, ya da ayarlar işleme kaybı olarak önümüze gelir. Ayrıca imalat esnasında kullanılacak ekipmanın olmaması, arızalı olması ya da eksik olması işleme kayıplarına yol açar.
- Üretilen ürün ya da hizmete müşterinin istemediği kalite özelliklerinin katılması için yapılanlar da kayıptır ve bundan kaçınmak gerekir.
- İşleme yönteminin kendisi de gereksiz kayıplara yol açan bir problem kaynağı olabilir.
-ÖRNEK; Püskürtme döküm işlemesi:
Döküm iyi yapılırsa sonraki yüzey taşlama işlemine gerek kalmaz.
-Diğer bir örnek; bir işlemde üzerinde fazla yağ bırakılan bir metal ürünü bir sonraki işlem olan tavlamada üzerindeki yağı uçurmak için daha fazla süre kalmak zorunda kalacaktır
- Üretim presesinde yapılacak bazı değişiklerle işleme kayıpları son derece düşürüleceği gibi üretilen mamullerde de yapılacak bazı değişikliklerle o işlem basamağı tamamen kaldırılabilir.
5.Stok Kaybı
“Fazla Üretim Kayıpları” ile aynı sonuçları doğurur.
Stokları Azaltmak için:
- Kullanılmayan malzemeleri ortadan kaldırmak (Bina bakım/İşyeri org.)
- 5S çalışması yapılmak.
- Bir sonraki süreçte lazım olmayacak ürünü üretmemek ,
- Hat Dengeleme çalışmaları yapılmalı. Sipariş miksi doğru tanımlanmalı, İyi planlama için standartlar doğru belirlenmeli.
- Malzemeyi büyük partiler halinde satın almamak.
- Ucuz olsun diye büyük partilerle alınan bazı malzemeler işgal ettiği saha, stok maliyetleri, zaman içinde aşınma bozulma v.b. nedenlerle gerçekte pahalıya gelebilir.
- Depo Yönetim Sistemi uygulamak
- Ürünleri küçük partiler halinde imal etmek.
Bu durumda set-up’ları süreleri daha önemli hale gelir. Bunu için SMED analizi yapılmalı.
Set-up sürelerin kısaltılması stok kayıplarının azalmasının yanı sıra, zamanında teslim, güvenli bir saha yönetimi ve üretim parametrelerinin kalite odaklı olmasını sağlar
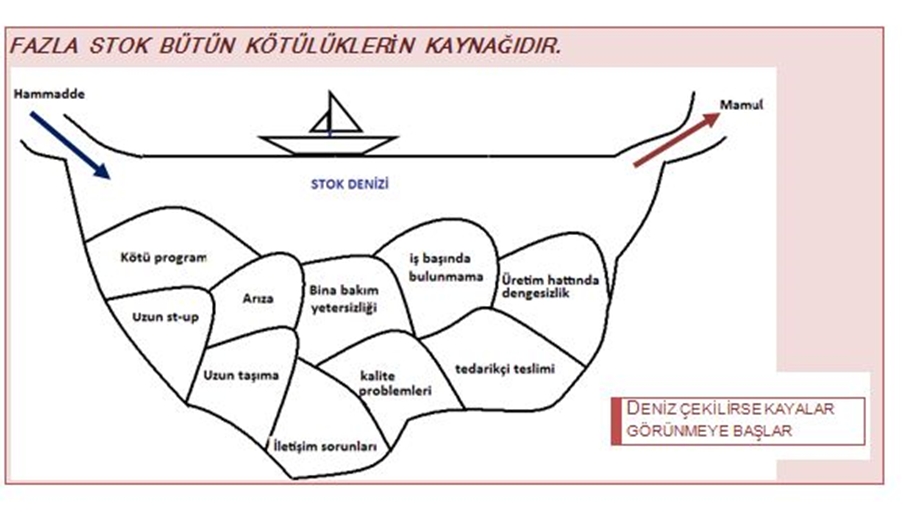
6.Hareket Kayıpları
Hareket her zaman işe dönüşmez. Ürüne değer katmayan hareket kayıptır.
Bir operatör ya da bakımcının fabrikada ya da depoda uzun süre malzeme ya da ekipman araması onu çalışıyor gibi gösterir ama gerçekte bize ya da ürüne hiçbir değer katmaz. Bu çok önemli bir kayıptır ve mutlaka önlenmelidir.
Fireyi seçme ve yerleştirme de bir kayıptır.
Bu nedenle fire ve hurdaları azaltmak gerekir. Fire için harcanan makine ve insan zamanı çok önemlidir. Kayıp bununla da kalmayıp bu fireleri incelemek, raporlamak, taşımak, stoklamak, tekrar işleme almak için yada hurda yapmak için taşımak ve stoklamak gerekecektir. Bunların hepsi kayıplarımızdır.
Yürüme de kayıpdır.
Makine yerleştirme, Saha düzenlemesi yapma, stok alanlarını düzenleme, hurda-ürün kova veya sehpa yerlerini düzenleme yürüme kayıplarını azaltır.
7.Ürün Kusurlarından Kaynaklanan Kayıp
Bir iş merkezinde kusurlu ürün çıkarsa takip eden iş merkezi bekler. Bu nedenle organizasyon makinelerin durmaması için ara stokları artırarak olabilecek kayıpları başka kayıplarla ortadan kaldırmaya yönelir.
Halbuki işi başından sıkı tutup “sıfır kusurlu ürün” hedeflenmelidir. Kaliteden ödün vermemek aslında birçok kaybı daha başından önler.
Aksi halde stokların artmasının yanı sıra inceleme ve yeniden işleme maliyetlerine de katlanılır.
Kusurlu ürünün müşteriden dönmesi daha da vahim sonuçlara yol açar. Yeniden işleme maliyetlerinin yanı sıra müşteri memnuniyetsizliği, fiyat rekabetinden geri düşme ve tazminat dibi çok önemli kayıplar maliyetlerimiz katlayarak artırır.
Montaj işlemi varsa sorun daha da büyür. Ürünün demonte edilmesi, yeniden üretilmesi sonrası tekrar montaj yapılması; bu tekrar montajda bazı parçaların değişmesi gerekliliği büyük kayıplara yol açar.
Kusurlu ürün kayıplarına katlanmamak için kusurlu ürün üreten koşulları belirleyecek ve önleyecek kişilerin ya da sistemin oluşturulması önerilmektedir. Bunun için insana bağlı koşullardan mümkün olduğunca kaçınmak gerekir. Bu mümkün değilse kalite ve proses parametrelerinin çok iyi tanımlanıp çalışanların bu standartları uygulaması sağlanmalıdır.
Gelecek yazımızda yukarıda anlatılan kayıpların ortadan kaldırılması için neler yapılabileceğini daha detaylı olarak örnekleri ile beraber anlatacağız.
Mustafa TOKA
Kaynakça: İmalatta Mükemmellik Yolu/ Kiyashi SUZAKİ